What are Galvanic baths and why are they needed
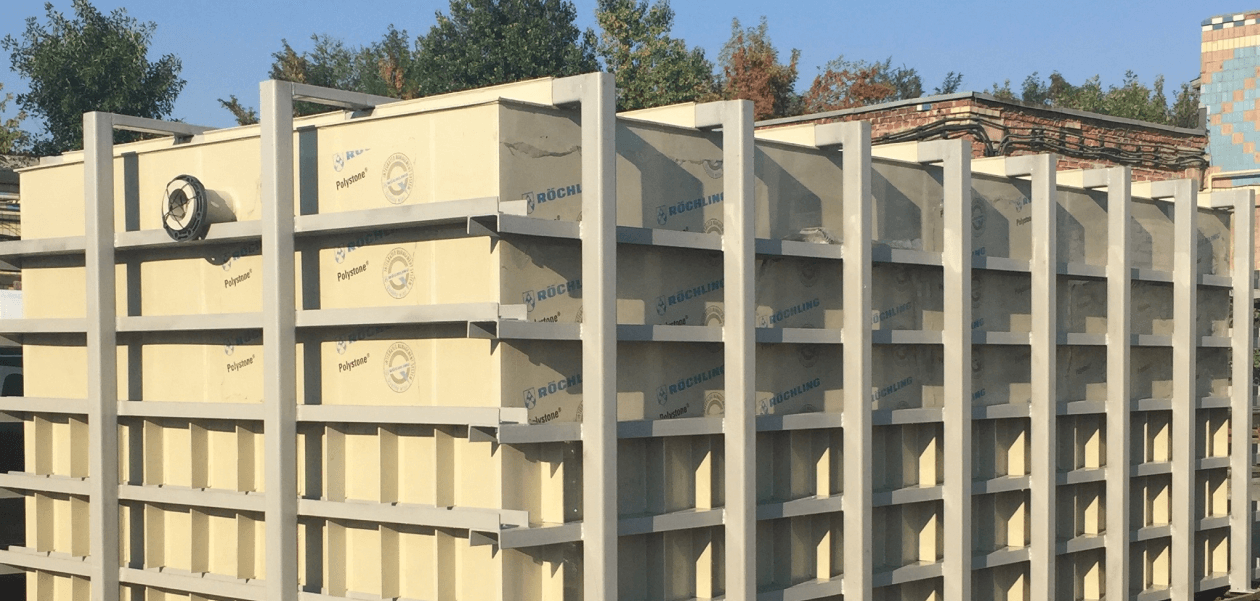
Modern production processes that use galvanic coating methods are metallurgy, mechanical engineering, electronics and a number of others. However, without proper equipment, it is impossible to achieve high efficiency and quality of application of protective and decorative layers. This is where galvanic baths come to the fore – specialized containers in which chemical and electrochemical processes of metal deposition take place.
Many people do not know how a galvanic bath works – the operating principle is based on an electrolytic process during which metals are deposited on the surface of the product from a solution under the influence of electric current. This allows not only to improve the appearance of the product, but also to significantly improve its performance characteristics:
- corrosion protection;
- wear resistance;
- improved conductivity;
- biocompatibility in the case of medical products.
Due to their versatility, galvanic baths are used to apply nickel, chromium, zinc, copper, silver and other metals.
Why do you need galvanic coating
Without using galvanic baths, companies may face a number of serious problems:
- Products are subject to rapid destruction due to corrosion, which reduces their service life and increases the cost of repair or replacement.
- The lack of a high-quality coating reduces the marketability of the product, which can affect its competitiveness in the market.
- Manual metal processing methods do not provide uniform application of the coating, which negatively affects the strength and functionality of the products.
How do galvanic baths solve these problems?
The main purpose of galvanic baths is to ensure efficient and uniform application of protective and decorative coatings. They allow you to achieve process accuracy, automate production and reduce the impact of the human factor. A modern galvanic bath is a well-thought-out design equipped with temperature control, filtration and electrolyte mixing systems, which makes the process more stable and predictable.
The use of galvanic baths also helps save materials. Due to electrochemical deposition, the metal is consumed strictly in the required amount, which reduces raw material costs and makes the process more environmentally friendly. Another advantage is the ability to create complex multilayer coatings that provide additional strength and resistance to aggressive environments.
Selecting the Right Galvanic Bath
The choice of the optimal galvanic bath depends on many factors, such as the type of metal, the size of the workpieces, the required coating characteristics and operating conditions. For example, for galvanizing, tanks with alkaline or acidic solutions are used, and for nickel plating – with special additives that improve the gloss and adhesion of the coating.
It is also worth considering the material from which the bath itself is made. Until recently, galvanic baths were containers made of metal and stainless steel. But recently, plastic models have become increasingly used, which have increased resistance to aggressive chemicals.
It is important to pay attention to the quality of manufacture, since a poor-quality bath can lead to leaks, uneven deposition of the coating and failure of the entire production process.
Features and advantages of plastic galvanic baths
Galvanic baths are important equipment in various industries, including electrochemical processes, metal coating, anodizing and electroplating. As already noted, plastic baths have recently become increasingly popular due to their many advantages over traditional metal counterparts. Namely:
- Plastic galvanic baths are made of chemically resistant polypropylene (PP), polyvinyl chloride (PVC), high-density polyethylene (HDPE) and fluoroplastic (PTFE). These polymers provide resistance to aggressive environments used in galvanic processes.
- The design and shape of the bath can be made according to individual customer requirements, taking into account the size, shape and additional elements, such as reinforced walls, built-in overflows and filtration systems. Plastic is easy to heat treat, which allows for the manufacture of complex configuration structures.
- Unlike metal analogues, plastic has low thermal conductivity, which allows for better maintenance of the temperature of solutions inside the bath. This reduces energy costs for heating the electrolyte.
- One of the main advantages of plastic baths is their high resistance to corrosion. Metal baths are subject to destruction under the influence of acids, alkalis and other chemicals, while plastic retains its properties for a long time.
- Modern plastics can withstand significant loads. With proper operation, the service life of galvanic baths made of polymer materials significantly exceeds the service life of metal analogues.
- Plastic baths are much lighter than metal ones, which simplifies their transportation, installation and replacement. In addition, they do not require complex welding work during installation.
- Hygiene and ease of maintenance are another plus of the equipment. Plastic does not accumulate deposits and dirt, it is easy to clean and disinfect. This is especially important when using baths in conditions that require high process purity.
- Although the initial cost of plastic baths may be higher, their performance characteristics provide significant savings on repair, maintenance and replacement of equipment.
Plastic galvanic baths ensure reliable and efficient operation of galvanic lines, reducing operating costs and increasing the safety of production processes. Due to the possibility of individual design, plastic baths can be adapted to any production requirements, which makes them the optimal choice for enterprises of various profiles.
Why is it worth ordering galvanic baths from KRAFT?
High-quality equipment is the key to efficient production. The specialized company KRAFT offers not only standard solutions, but also the manufacture of galvanic baths for specific customer tasks. This allows you to take into account the specifics of production, optimize material consumption and improve the quality of finished products.
If you need reliable and durable equipment, pay attention to custom-made plastic containers. They have high chemical resistance, durability and ease of use. When ordering equipment from a trusted manufacturer, you receive a quality guarantee, technical support and the ability to customize the system to the individual needs of your production.
It will also be interesting
Do you need a consultation?
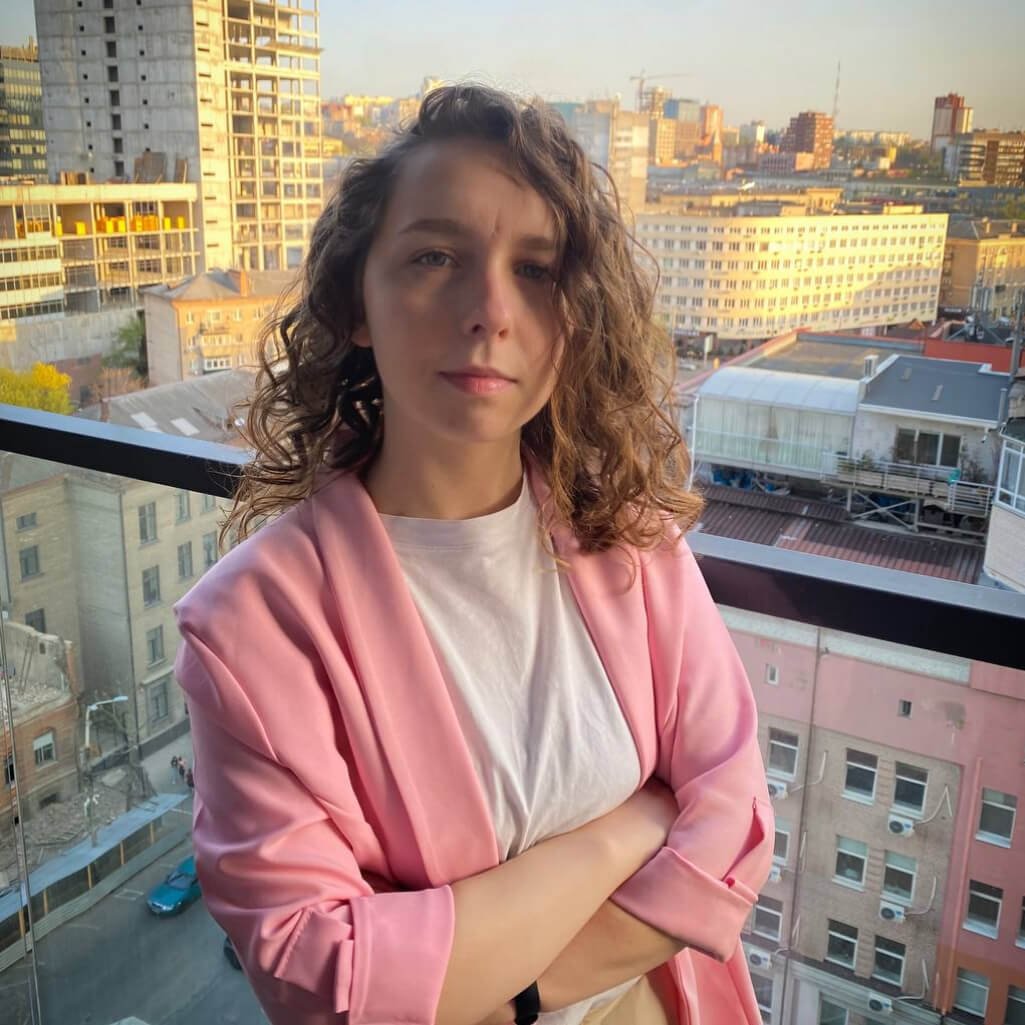
Sales Manager
Alexandra
Fill out the form and we will be in touch to answer your questions